8 Factors to Consider When Evaluating Bonded Laminates
Make an informed decision when selecting bonded laminates for your cladding project. Here’s a comprehensive checklist of 8 key factors you need to consider.
Are you planning to use bonded laminates for your cladding or recladding project?
Also known as aluminium composite panels, bonded laminates are composed of two or more layers of different materials that are integrated into a single structure, enhancing the:
- visual appearance
- durability, and
- performance of a building’s external facade.
There are multiple types of bonded laminates available in the market, and each one offers its own set of unique characteristics and benefits that you can leverage for your specific project.
So, to ensure a successful cladding outcome, we have prepared a practical checklist of 8 factors to consider when selecting the right bonded laminates for your building.
Let’s explore these key considerations you need to keep in mind.
What are the important aspects to consider when evaluating bonded laminates?
Here are some guide questions to help you make a well-informed cladding material decision.
1. What type of core do these bonded laminates have?
Bonded laminates are often made of a core material ‘sandwiched’ between two thin aluminium sheets.
This core comes in different forms, including corrugated, honeycomb and non-combustible mineral.
Bonded laminates with corrugated and honeycomb cores have air pockets, making them lightweight and more manageable to use.
On the other hand, bonded laminates with a mineral core are recognised for their strength and rigidity. Due to the non-combustible mineral core, these bonded laminates are also the safest.
Just remember: the core material of bonded laminates is a crucial element to the overall safety and performance of cladding panels.
As such, Building Owners, Architects, Builders and Consultants should take this into account when determining what kind of bonded laminates to use for your property, building or project requirements.
2. Are these bonded laminates compliant with safety regulations here in Australia and abroad?
Whether you are completing a new commercial project, multi-residential property or high-rise building, or working on a recladding project, it’s necessary to use high-quality materials that promote safety.
With this, your bonded laminates should be able to:
- meet building code requirements,
- obtain local certifications needed, and
- be tested to the AS 5113 large-scale facade fire test.
Consider ALPOLIC™ NC/A1 as an example.
ALPOLIC™ NC/A1, distinguished by its mineral core, has received recognition from the Insurance Council of Australia for achieving the highest possible safety rating as a cladding product.
It has also undergone rigorous large-scale fire tests, including AS 5113. Furthermore, ALPOLIC™ NC/A1 stands as the only aluminium composite material to pass Euroclass A1 certification – the strictest fire protection standard in the world.
3. How will these bonded laminates perform in extreme weather conditions?
One of the main purposes of cladding is to protect your building against harsh external elements such as hail, rain, wind and UV radiation.
As such, your primary concern should be to choose bonded laminates that can prevent your property from easily deteriorating, especially against adverse weather and climate change.
The question now is – which type of bonded laminates should you use?
Bonded laminates with a mineral core are characterised by their strength, durability and resilience.
Because they are less prone to denting or failing when subjected to any kind of impact or pressure, these bonded laminates are a dependable choice for environments exposed to extreme weather conditions.
Conversely, bonded laminates with a corrugated or honeycomb core have a much higher likelihood of denting or failing in extreme weather. The presence of air pockets within their structure makes them lighter, but also more susceptible to damage and less resilient to impact forces such as hail.
In fact, there are reported instances in Australia where corrugated or honeycomb core panels are being replaced due to the damage they’ve sustained from previous hailstorms.
![]() |
![]() |
4. Do these bonded laminates require ongoing maintenance?
The answer to this question depends a lot on the coating of the aluminium protecting the core of the bonded laminates, rather than the core itself.
Some bonded laminates come with a Lumiflon FEVE coating (or a fluoroethylene vinyl ether resin-based powder coating) that not only preserves the depth and lustre of cladding panels but also significantly extends their durability.
As a result, these bonded laminates won’t need regular cleaning or maintenance to ensure their long-lasting design.
In contrast, bonded laminates with a PVDF resin-based coating must be cleaned to maintain their warranty. Make sure you choose the right one based on maintenance requirements.
5. What does their bonded laminates warranty include?
When searching for the right bonded laminates for your project, make sure you check if they offer a long-term manufacturer’s warranty. After all, you don’t want to deal with costly defects and expensive repairs in the near future.
Consider also whether the warranty covers material, labour and rectification costs for faulty materials, as well as if it stipulates no cleaning requirements for maintenance.
The warranty of your bonded laminates should also be backed by the product’s manufacturer, which has the resources and expertise to solve any issue not only today but also in the years to come.
Unfortunately, warranties aren’t much good if the organisation behind them doesn’t exist any longer when you need to make a claim. A strong manufacturer’s warranty gives you more protection long-term.
To learn more about cladding product warranties, here are 6 important questions you need to ask.
6. How do these bonded laminates compare in price?
Quality bonded laminates are not cheap, but they allow you to meet safety, durability and aesthetics requirements, providing you with more value for your investment.
So, when assessing bonded laminates, make sure you take into account the factors that go into pricing, such as:
- suitability of the panels for their intended purposes,
- compliance with building regulations,
- ongoing maintenance costs, and
- potential risks for repairs.
- the warranty
Always remember – you get what you pay for.
Instead of finding the cheapest cladding alternative, it’s recommended to focus on choosing the right products that will provide you the highest return in the long run.
7. Are these bonded laminates sustainable in the long run?
Clients are now placing sustainability as one of their top priorities when it comes to building projects. As a Building Owner, Architect or Builder, you are then often expected to use materials that contribute to sustainable practices.
Fortunately, there are bonded laminates that are environmentally friendly.
Mitsubishi ALPOLIC™ NC/A1, for instance, is 100% recyclable and produced with less energy than solid aluminium. It also has thermal insulation properties that help in boosting the energy conservation performance of any building.
As evident in their successful registration of Environmental Product Declarations (EPDs), all production plants of ALPOLIC™ by Mitsubishi Chemical Infratec Co., Ltd are also compliant with ISO14001 – the international standard for environmental management systems.
8. Who is the manufacturer of these bonded laminates?
To get the best results from cladding, it’s ideal to use bonded laminates that are manufactured by a reputable and trusted company – as mentioned in the warranty consideration.
Credible manufacturers have an excellent reputation for delivering the highest standards of quality and service when it comes to their products.
They also have a team of skilled professionals who can provide expert guidance and cladding product support when choosing the right type of bonded laminates for your unique requirements.
With the right bonded laminates manufacturer, you can ensure the effectiveness, durability and longevity of your cladding system.
ALPOLIC™ NC/A1: A product that satisfies all 8 of these important considerations
Are you looking for the ideal bonded laminates for your project?
At Network Architectural, we stock fire-safe and compliant bonded laminates that tick all of your requirements to make this decision simple.
ALPOLIC™ NC/A1, composed of a non-combustible mineral core is scientifically proven to be the safest aluminium facade product in large-scale fire tests around the world.
This aluminium cladding material is not only easy to process and shape, but is also weather-resistant, impact-resistant, has superior flatness and proven coating durability in Australian conditions for over 30 years.
Aside from its extraordinary safety and sustainability profile, ALPOLIC™ NC/A1 comes with an industry-leading 20-year FULL manufacturer’s replacement warranty that covers material, labour and rectification costs for faulty materials. And, unlike other products, it does not require costly maintenance to maintain the warranty.
Do you want your cladding or recladding project to be a complete success?
Whether you have more questions about recladding or are looking for the right cladding solutions for your project, we’ve got you covered.
Reach out to us and our team of facade experts can help you achieve the results you require.
As always, it’s best to seek the expertise of a trusted and well-established cladding supplier that can provide you with the highest standard of products.
At Network Architectural, we look forward to becoming your design and specification partner.
Related Articles
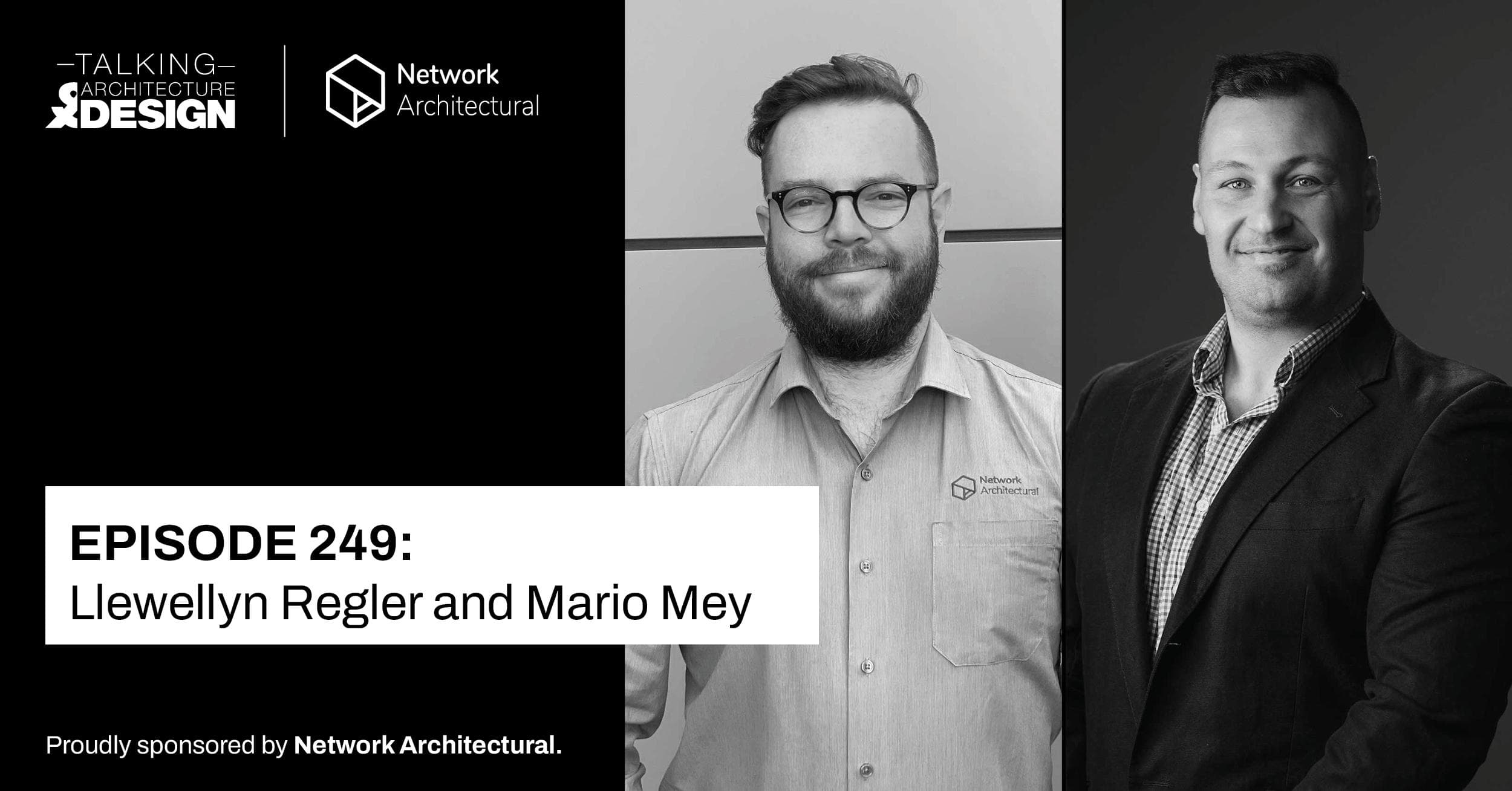
The Cladding Conversation: Facade Engineers Shouldn’t be an Afterthought
In this episode of Talking Architecture & Design, Total Building Engineering Solutions’ Mario Mey and Network Architectural’s Llewellyn Regler explore why engaging Facade Engineers early in a project is essential—not optional. From fire safety and waterproofing to the benefits of using ALPOLIC™ cladding, they discuss the evolving cladding landscape, the impact of the DBP Act, and the future of safe, high-performing facades.
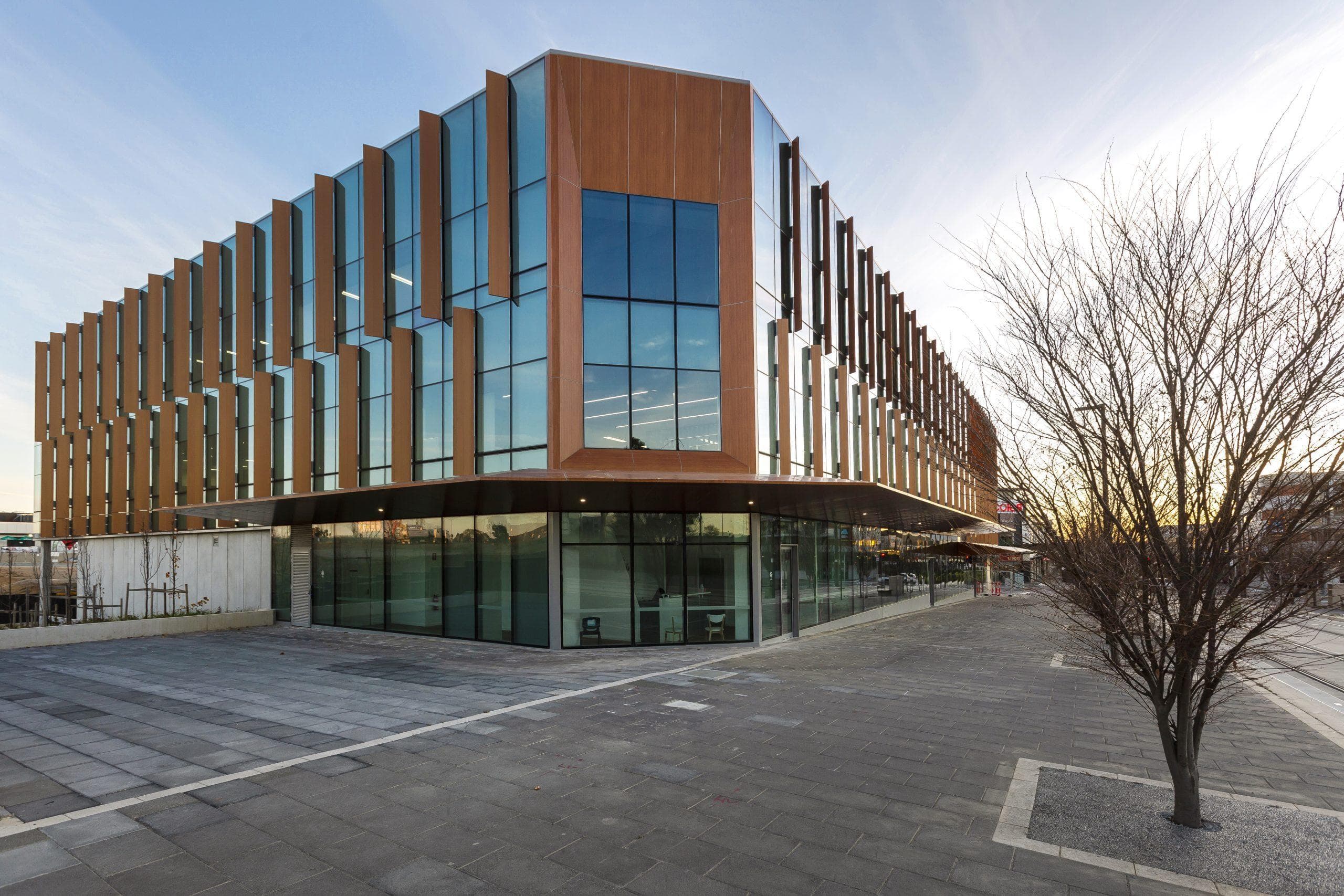
Engineering Resilient Facades
Australia’s extreme climate demands durable facades that ensure safety, performance, and longevity. This whitepaper explores key compliance standards and material solutions, designed to withstand harsh weather and thermal expansion.
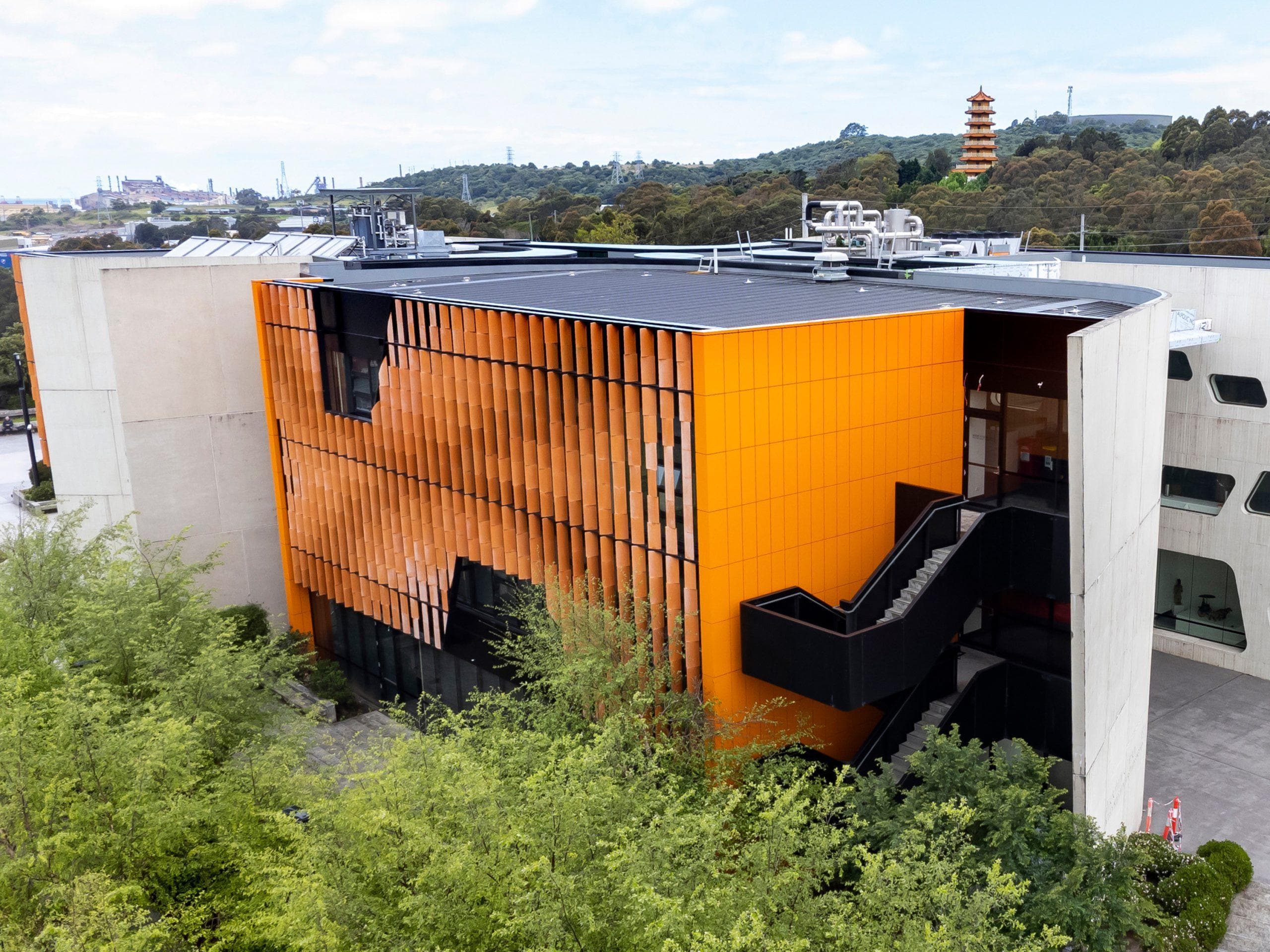
Sustainability eBook 2024
For the third year in a row, Network Architectural was proud to sponsor the Commercial Architecture (Large) category for Architecture & Design’s Sustainability Awards 2024.